Squeal analysis is a significant part of SDTools activities. It is a type of friction induced instability occurring in braking devices. Main applications are automotive, but a wider class of subjects exist everywhere a friction-based mechanism is designed (wind turbine brakes, polishing, machining, sleeve guides, …).
Based on a 17 years’ experience in squeal applications, SDTools continuously develops a series of tools adapted to the analysis of experimental squeal measurements, simulation, and countermeasure design [1,12]. These tools are used for consulting but can also be deployed in customers processes under the form of application tools (GUI or script based). Recently, module SDT-Squeal has been released to integrate usual simulation processes used in our consulting activities.
Squeal signal analysis
SDTools is developing a series of tool to automatically extract features from transient squeal signals (experimental or simulated). Besides data compression from raw results, the features are engineered to be physically representative of parameters at stake in the system. Preliminary work can be found in [2]
The SDT-Squeal module: frequency domain analysis
Frequency domain analysis is a common step for brake squeal simulation. The computation of unstable complex modes in the sense of Lyapounov is a preliminary step to assess the system behavior. The underlying deformation modes provides kinematic reduction bases and an understanding of the mechanisms at play for squeal trigger [1].
As many parameters are at play, model updating from correlation and the search for countermeasures imply running large experiments with many parameters [3,4,5]. These are made possible in the module with the help of parameterized reduced multi-models, that allow simulating state-of-the art industrial brake models over 10,000 design points in hours.
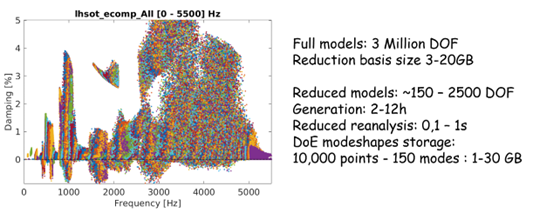
When running large scale design of experiments one has the possibility to track modes and understand how mode-shapes evolve as function of the parameters. Dedicated tools are however required to aggregate data. Pole clustering techniques have thus been developed to aggregate mode-shapes by distance with the kinetic energy norm [3].
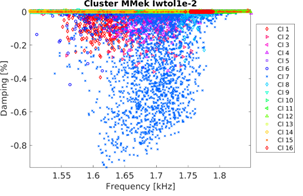
Parameter regression can then be perform to analyze trends and sensitive parameters for a given objective.
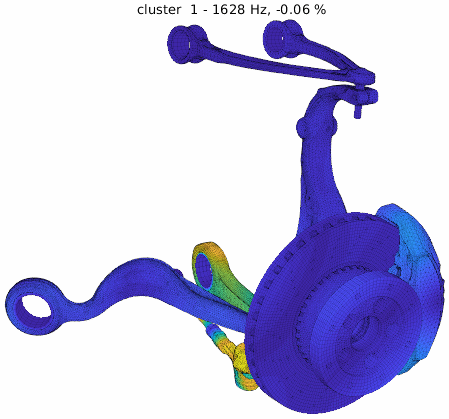
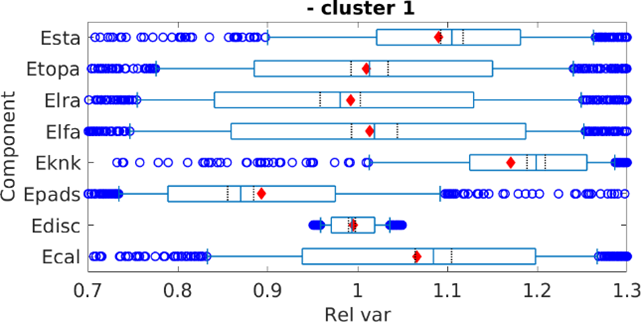
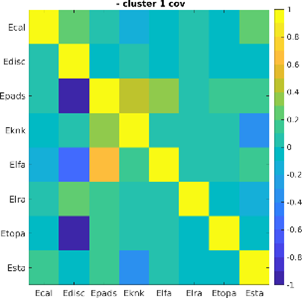
Advanced tools: component contributions
Brakes are complicated assemblies of a dozen main components for a quarter vehicle model. Understanding modeshapes and their sensitivity for design based analysis is eased by the Component Mode Tuning (CMT) framework that uses component free modes as explicit Degrees of Freedom (DOF) [3,6,7,8]. These analyses can also be applied on cluster shapes and provide insightful design oriented analyses for updating and countermeasures.
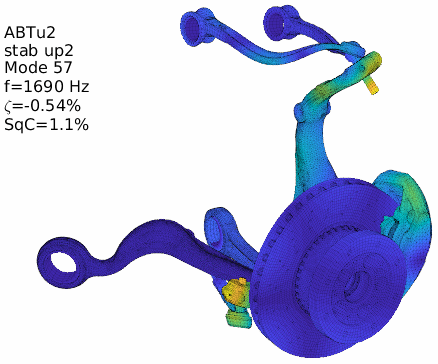
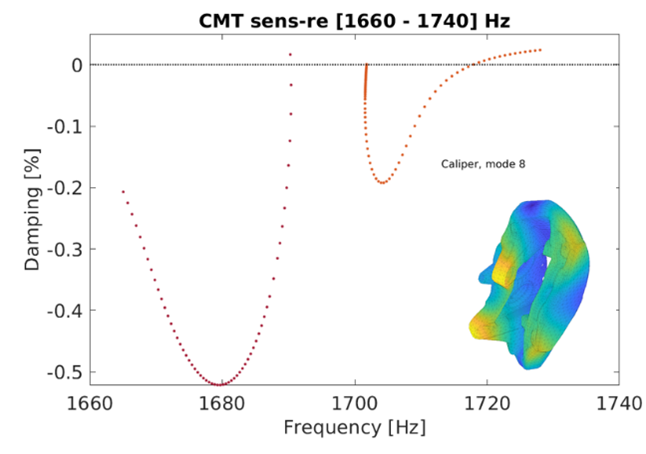
Advanced tools: Expansion and correlation with metrics
One of the major challenges with large models resides in their quality. Correlation tools are used to proceed on model validation from experimental measurements. SDTools expansion tools featuring the Minimum Dynamic Residue Error (MDRE) method provides an efficient way of estimating the expansion of an experimental shape on the model, with error indicators [9,10,11]. Analysis of the expanded shape provides a great insight on potential issues in the model while the indicators can be used to run optimization procedures. Integration of parameterized reduced multi-models has been developed to link the usual frequency-based sensitivity studies with expansion error [8].
Thanks to our past and present partners
References
[1] From transient simulation to extended complex mode analysis. Squeal simulation of an industrial automotive brake
[2] Parametric modal testing using slow but continuous variation of operating conditions. Illustration on a contact bench.
[3] Efficient Large Multi-Parametric Squeal Simulation And Analysis Using Advanced Model Reduction Tools
[4]Reduced order brake models to study the effect of squeal of pad redesign
[5] Squeal complex eigenvalue analysis, advanced damping models and error control
[6] The Component Mode Tuning (CMT) method. A strategy adapted to the design of assemblies applied to industrial brake squeal.
[7] Using component modes in a system design process
[8] Model Quality Quantification And Improvement Based On Operational Squeal Deflection Shapes Expansion
[9] Expansion in structural dynamics: a perspective gained from success and errors in test/FEM twin building
[10] A Structural Dynamics Modification Strategy based on Expanded Squeal Operational Deflection Shapes
[11] MDRE: An efficient expansion tool to perform model updating from squeal measurements
[12] Benchmarking Signorini and exponential contact laws for an industrial train brake squeal application