How to perform modal analysis of milling robot using a spindle-driven unbalanced excitation ?
SDTools is a partner in a research project aiming to characterize the dynamic properties of a machining robot.
Experimental modal analysis based on impact hammer testing would be a classical method, but it does not consider the influence of spindle rotation or cutting forces on system dynamics. For this, an operational modal analysis could be performed, but it would require extensive instrumentation.
This project proposes an intermediate method: Excitation using eccentric masses that generate force with spindle rotation
Excitation frequency sweep by slowly increasing the rotation frequency
Estimation of transfers : output sensors responses to input force
Highlighting of non-linearities with several masses generating different levels of excitation
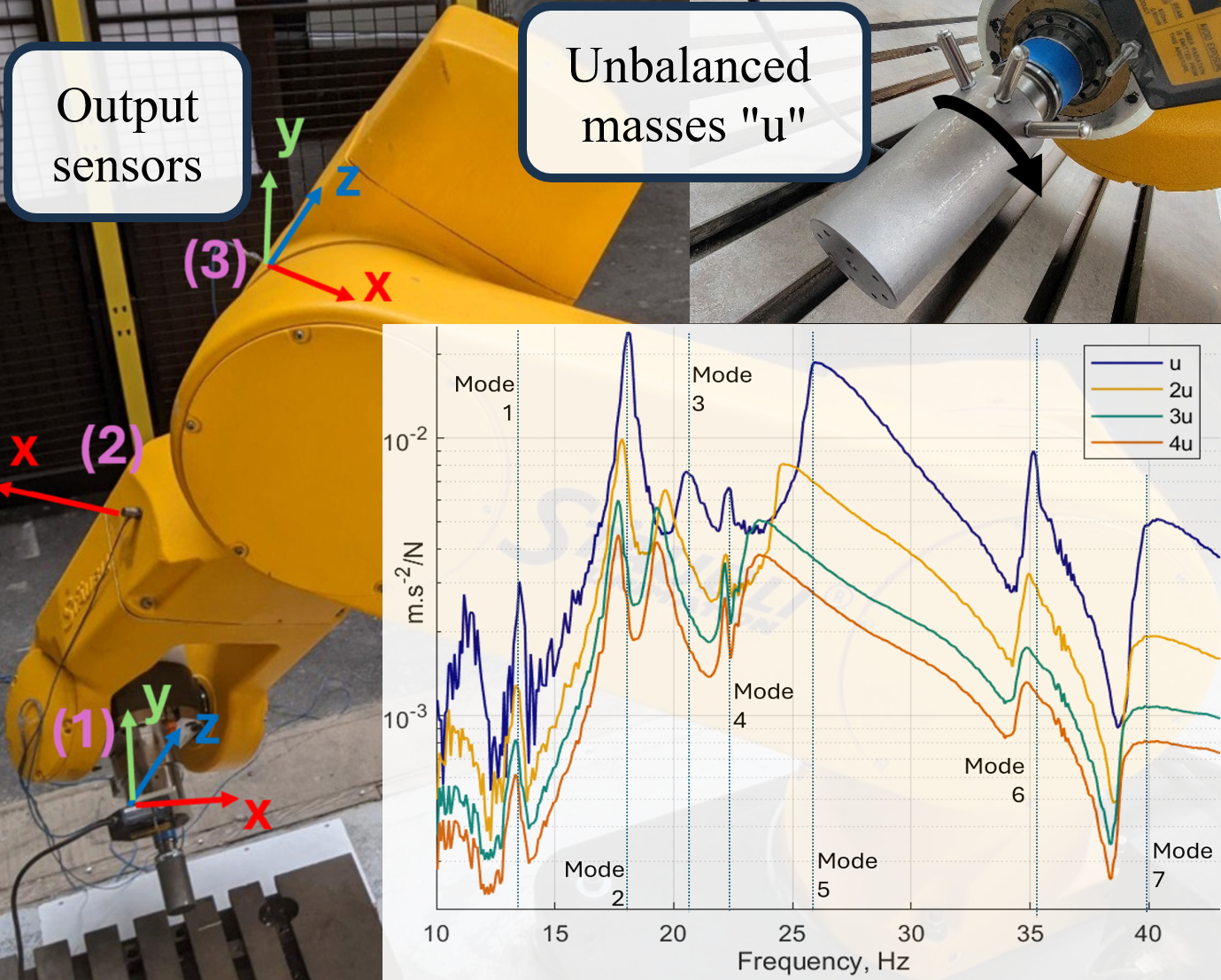
Evolution of transfers with increasing mass.
SDT was used to estimate transfers using a recently developed method where an HBV (Harmonic Balanced Vector) signal model is estimated using demodulation.
We will come back to the principle of this method in a later post !
The initial results of this project were the subject of a conference paper at ISMA2024.
Grigorii Altshul will present this work during the poster session on Wednesday 11/09 at 8:30
Summary:
“This article presents a novel modal analysis method for investigating the dynamic behavior of milling robots. The proposed method utilizes inertial forces generated by an unbalanced tool rotating on the spindle to excite vibrations, and the frequency response function (FRF) is obtained through demodulation of the recorded vibrations. The study demonstrates the evolution of the robot’s FRF with varying levels of unbalance, showing that the modes exhibit softening behavior and increased damping as the unbalance increases. The method offers a balance between simplicity and precision, requiring less instrumentation than operational modal analysis (OMA) methods while allowing for controlled excitation levels. The importance of precise spindle rotation speed data is highlighted, suggesting the benefits of using spindles with encoders for better results. This method can be applied for characterization of robots in different poses, addressing non-linear behavior significant for the robot’s role in milling processes.” Authors: Grigorii Altshul, Mikhail Guskov, Etienne Balmes and Philippe Lorong